Membrane Switches
Membrane Switches
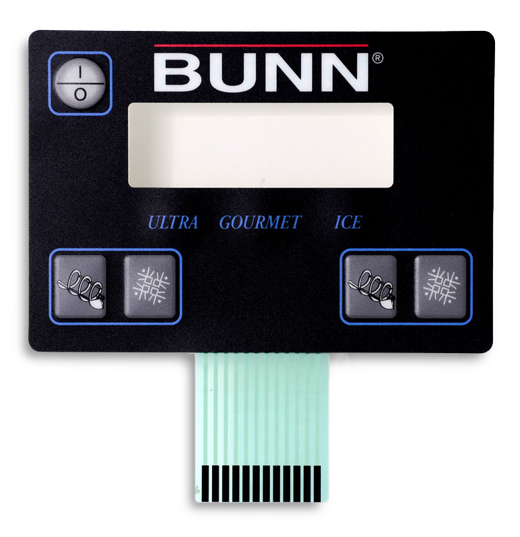
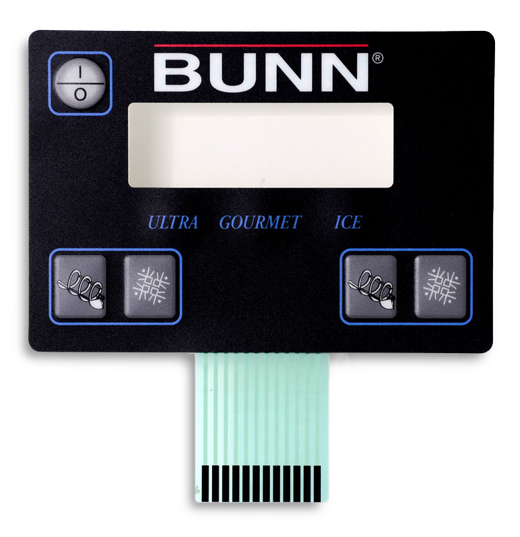
What Are Membrane Switches?
The easiest way to understand what a membrane switch is, is to reference an all-time favorite device-the microwave. The membrane switch on the microwave is the buttons—the human interface layer—that communicates to the microwave that you’d like to reheat your food for one minute.
At Nelson-Miller, we specialize in manufacturing membrane switch solutions with demanding reliability and stringent cosmetic requirements. We are proud to be industry leaders in producing membrane switches that meet or exceed our customers’ expectations. Our Los Angeles based state-of-the-art manufacturing facility supports a variety of processes to bring you the best custom membrane switches in the market today. Some of the processes include: screen and digital printing, color matching, die cutting and laser fabrication, laminating processes, clean-room membrane switch assembly, as well as environmental and life cycle testing.
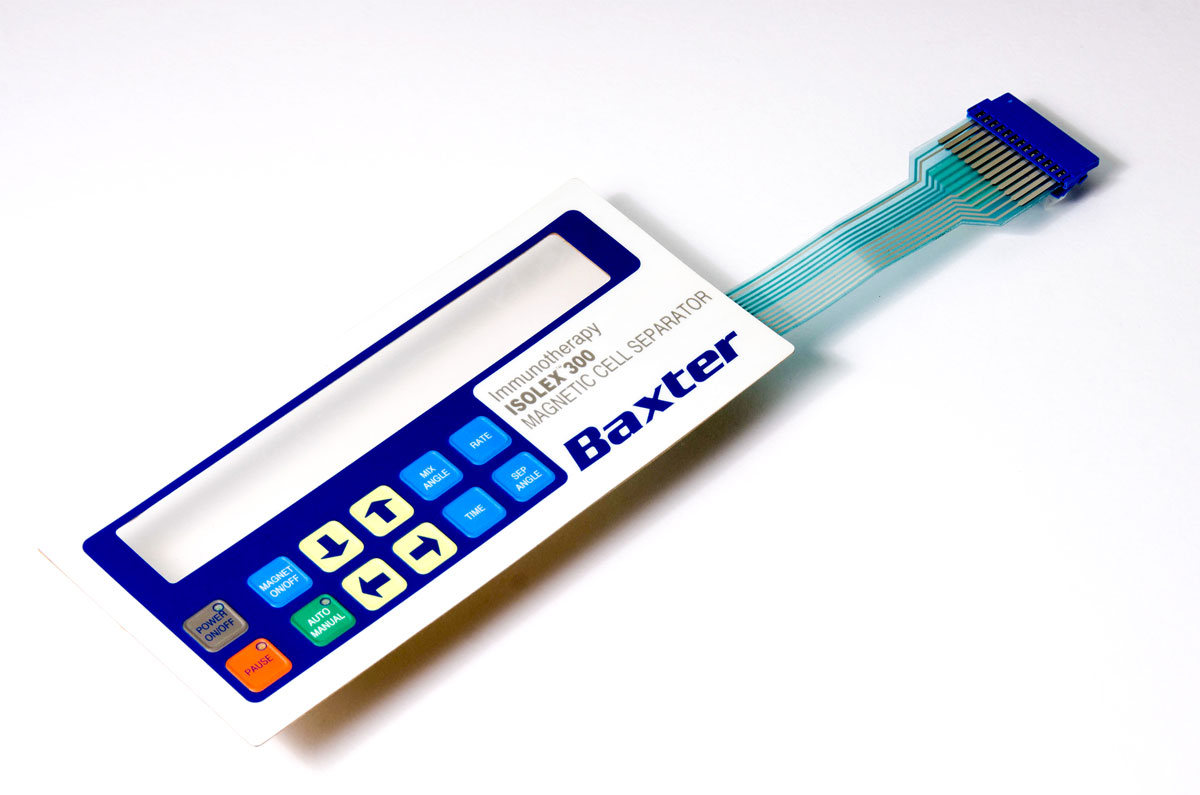
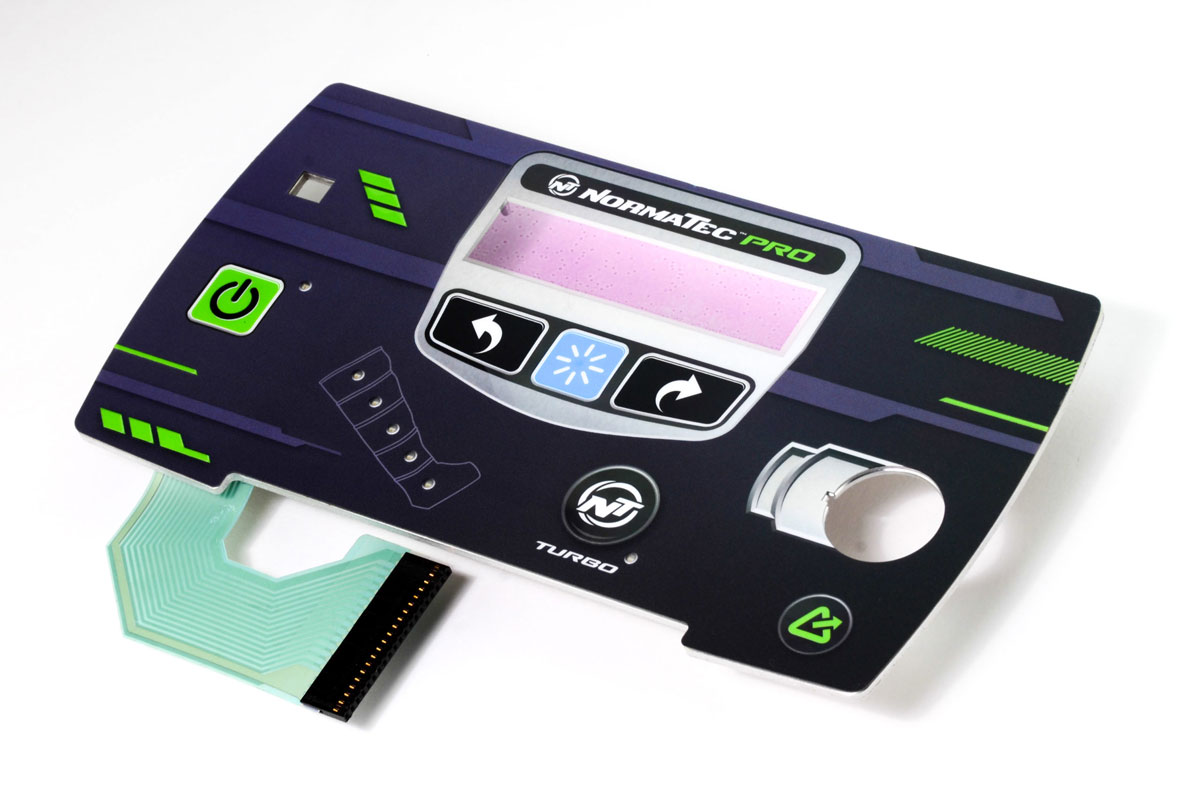
Membrane switch construction
A membrane switch consists of various layers laminated together. The layers of a basic membrane switch construction include: a membrane overlay, spacer, printer circuit, rear adhesive, and tail filler. Depending on the environment and requirements of the application into which the membrane switch plugs into, the construction can vary. For example, if shielding is necessary, a two-circuit membrane switch design would be a better construction choice.
For more stringent environmental requirements, the printed silver circuit can be replaced with a copper and polyimide construction. These construction designs are often called “Kapton” circuits and offer advantage with regard to current carrying capacity and better resistance to moisture. You can explore more construction possibilities by downloading our membrane switch design guide or contacting us for support.
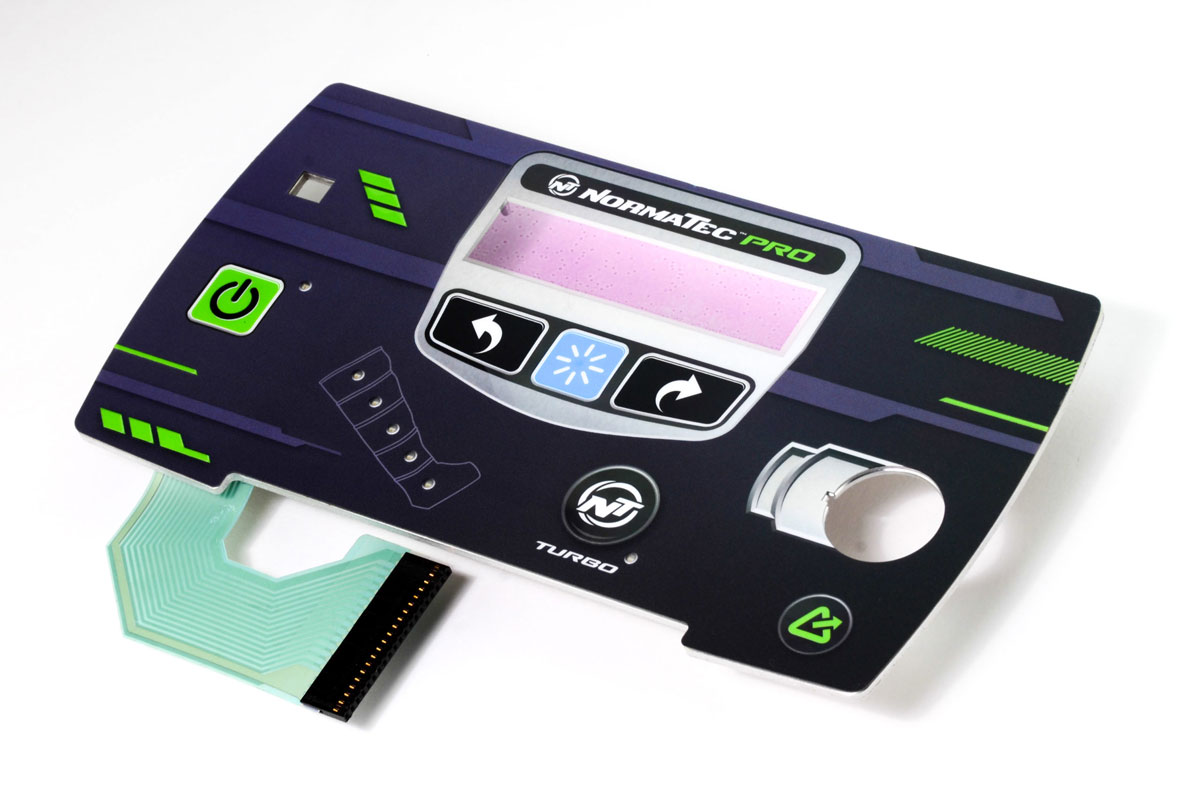
What Industries Use Membrane Switches?
There are a variety of industries that use membrane switch applications. One example would be the medical industry. Membrane switches for the medical industry must comply with strict FDA standards; they must be reliable, use high quality metal domes with correct plating, and eliminate crossover on circuits in extreme environments, as people’s lives literally depend on them. The membrane keypads must be well sealed and moisture protected against liquid spills and cleaning solutions. Some medical professionals prefer their medical devices to have lower tactile force but high tactile feel. This requires good design and proper material selection in order for the latest dome designs to be successful.
- Medical Devices
- Aerospace
- Defense / Military
- Consumer
- Industrial
- Gaming